Injection molding process:
Injection molding is the most common modern method of manufacturing plastic parts; it is ideal for producing and modify composite magnetic materials to appeal to specific application.
Injection Molding magnet:
Isotropic material– the magnetized coil fixture design determines the magnetic material it takes.
Anisotropic type requires for the external magnetic flux, to set magnetic domain for magnetic powder in the polymer. For the sake of cost reduction, injection molded magnets are produced in tens or hundreds of thousands of magnets per production run.
Magnetfirm is specialized in the field of injection molding of magnets and have long experience in (PA)polyamide modified.

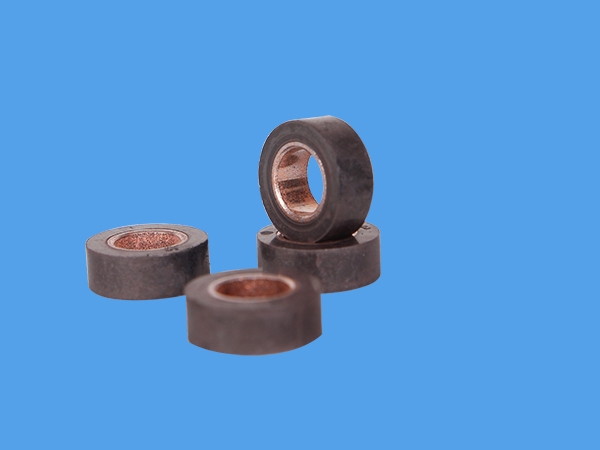
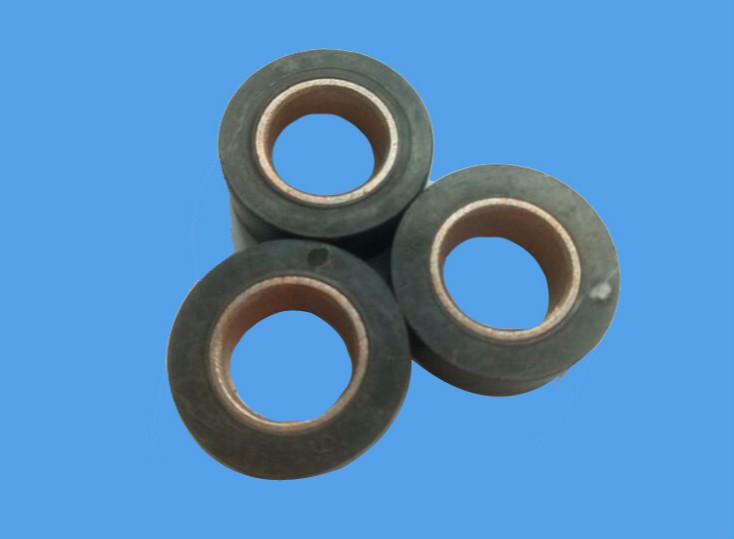
Applications of Injection Molded Magnet
- Motors
- Sensors
- Injection molded rotor assemblies
- Insert molded magnetic components
- Over molding magnetic components
- Medical pump magnet